La soldadura por arco se erige como un proceso fundamental en los ámbitos de la manufactura y la fabricación, facilitando la unión de materiales metálicos con una amplia gama de aplicaciones industriales.1 Dentro de las diversas técnicas de soldadura por arco, la Soldadura por Arco Metálico con Gas (GMAW, por sus siglas en inglés) se distingue por su extensa utilización, ofreciendo versatilidad y eficiencia en la unión de metales.1 Dos de las variantes primordiales dentro de la GMAW son la soldadura MIG (Metal Inert Gas, o Gas Inerte Metálico) y la soldadura MAG (Metal Active Gas, o Gas Activo Metálico).1 El presente informe tiene como objetivo principal dilucidar las diferencias fundamentales entre la soldadura MIG y MAG, abordando sus respectivos procesos, aplicaciones características, ventajas distintivas y desventajas inherentes. La comprensión detallada de estas diferencias resulta esencial para la selección del método de soldadura óptimo en función de los requerimientos específicos de cada proyecto.
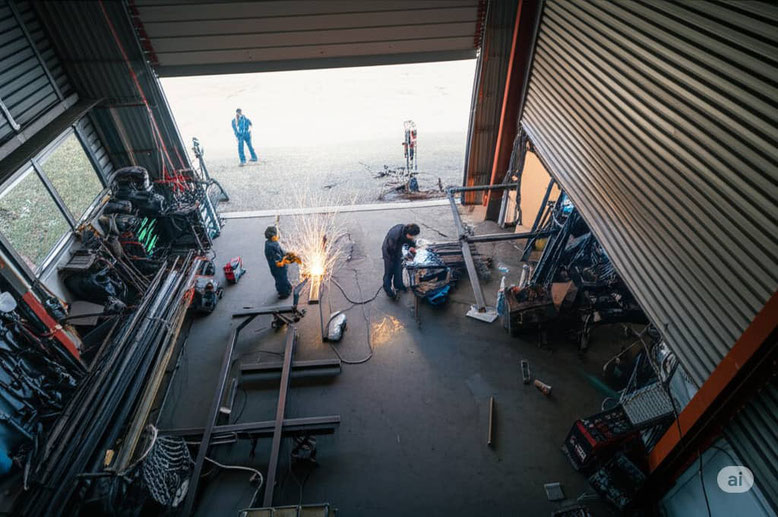
Fundamentos de la Soldadura por Arco Metálico con Gas (GMAW)
Tanto la soldadura MIG como la MAG se engloban dentro de la categoría de la soldadura por arco metálico con gas (GMAW).1 El proceso básico de GMAW implica la formación de un arco eléctrico entre un electrodo de hilo consumible, alimentado de manera continua, y la pieza de trabajo.1 El calor generado por este arco funde tanto el electrodo como el material base, lo que resulta en la creación de una soldadura al solidificarse el metal fundido.1 Para llevar a cabo este proceso, se requiere un sistema GMAW compuesto por varios elementos clave, que incluyen una fuente de energía que suministra la corriente eléctrica necesaria para generar el arco, un alimentador de hilo que asegura el suministro constante del electrodo consumible, una pistola o antorcha de soldadura a través de la cual se alimenta el hilo y el gas de protección, y una fuente de suministro del gas de protección.3 Es importante destacar que dentro del proceso GMAW, existen diferentes modos de transferencia del metal fundido desde el electrodo a la pieza de trabajo. Estos modos, que pueden ser por cortocircuito, globular, pulverización (spray) o pulsado, influyen significativamente en las características finales de la soldadura y son aplicables tanto a la soldadura MIG como a la MAG.3 La selección del modo de transferencia depende de los parámetros de soldadura, como el voltaje y la corriente, así como del tipo de gas de protección utilizado, lo que a su vez afecta la penetración y la cantidad de salpicaduras generadas.20
La Diferencia Fundamental: El Gas de Protección
La distinción primordial entre la soldadura MIG y la MAG radica en la naturaleza del gas de protección empleado durante el proceso.3 El gas de protección desempeña un papel crucial al rodear el arco eléctrico y el baño de soldadura fundido, protegiéndolos de la contaminación atmosférica.1 Esta contaminación, principalmente por oxígeno, nitrógeno e hidrógeno presentes en el aire, puede generar porosidad y debilitar la unión soldada. En este contexto, los gases de protección se clasifican en dos categorías principales: inertes y activos. Los gases inertes se caracterizan por su falta de reactividad química con el baño de soldadura fundido, manteniendo una atmósfera estable alrededor del arco.1 Por otro lado, los gases activos sí interactúan químicamente con el baño de soldadura, influyendo en las propiedades metalúrgicas y las características del cordón de soldadura.1 La elección entre un gas inerte o activo es fundamental para determinar si el proceso se denomina MIG o MAG, y esta selección se basa principalmente en el tipo de material que se va a soldar y las propiedades deseadas para la soldadura final.3
Soldadura MIG (Metal Inert Gas)
A. Proceso y Gases Inertes:
La soldadura MIG, o soldadura con gas inerte metálico, es un proceso GMAW que emplea un gas de protección inerte para proteger la zona de soldadura de la contaminación atmosférica.1 Los gases inertes más comúnmente utilizados en la soldadura MIG son el argón (Ar) y el helio (He).3 El argón se caracteriza por proporcionar un arco estable y es particularmente adecuado para la soldadura de metales no ferrosos, aunque también se utiliza en mezclas con otros gases para optimizar el proceso en ciertos materiales.3 Por otro lado, el helio genera un arco más caliente, lo que resulta en una mejor penetración, especialmente en secciones más gruesas y en metales con alta conductividad térmica, como el aluminio y el cobre. Debido a sus propiedades, el helio a menudo se mezcla con argón para combinar las ventajas de ambos gases.3 La elección específica del gas inerte o la mezcla de gases se determina cuidadosamente en función del tipo de material que se va a soldar, buscando la protección óptima del baño de soldadura y las características deseadas en la unión final.
B. Aplicaciones Comunes de la Soldadura MIG:
La soldadura MIG se considera ideal para la soldadura de metales no ferrosos.3 Un ejemplo destacado es el aluminio, cuya soldadura se realiza ampliamente utilizando argón como gas de protección.1 El acero inoxidable es otro material comúnmente soldado con MIG, utilizando a menudo mezclas de argón con dióxido de carbono o con oxígeno, manteniendo un bajo contenido de agentes oxidantes para prevenir la pérdida de cromo, elemento crucial para la resistencia a la corrosión.1 Otros metales que se sueldan eficazmente con MIG incluyen el cobre, el magnesio, el titanio y las aleaciones de níquel.1 En términos de aplicaciones industriales específicas, la soldadura MIG es extensamente utilizada en la industria automotriz, especialmente para la fabricación de componentes de aluminio.1 También es fundamental en la ingeniería aeroespacial, donde se requiere la unión de materiales ligeros y resistentes.33 La industria alimentaria y farmacéutica también se beneficia de la soldadura MIG debido a la limpieza de las soldaduras que produce.28 Adicionalmente, se aplica en la fabricación de estructuras metálicas y en la soldadura de chapa fina.
C. Ventajas de la Soldadura MIG:
La soldadura MIG presenta varias ventajas significativas, entre las que se destaca la producción de soldaduras más limpias y con menos salpicaduras en comparación con la soldadura MAG, gracias al uso de gases inertes que no reaccionan con el metal fundido.1 Generalmente, las soldaduras MIG ofrecen una alta calidad y a menudo presentan una mejor apariencia estética.7 Además, se considera un proceso relativamente fácil de aprender y operar, lo que lo hace accesible incluso para soldadores principiantes.1 Aunque tradicionalmente se ha asociado con la soldadura de materiales más delgados, los avances en la tecnología han permitido su aplicación en materiales de mayor espesor.1 La soldadura MIG es versátil y aplicable a una amplia gama de metales, principalmente no ferrosos, como se mencionó anteriormente.1 La alimentación continua del hilo de soldadura permite realizar soldaduras más largas sin interrupciones frecuentes, lo que se traduce en una mayor productividad.6 Finalmente, el proceso MIG se presta fácilmente a la automatización y la soldadura robótica, lo que incrementa aún más su eficiencia en entornos de producción a gran escala.
D. Desventajas de la Soldadura MIG:
A pesar de sus numerosas ventajas, la soldadura MIG también presenta ciertas desventajas. El costo de los gases inertes, como el argón y el helio, suele ser más elevado en comparación con los gases activos utilizados en la soldadura MAG, como el dióxido de carbono.22 En algunos casos, puede resultar menos eficiente para soldar materiales de gran espesor en comparación con la soldadura MAG, que ofrece una mejor penetración en aceros gruesos.20 Aunque generalmente se considera más fácil de aprender que otros métodos como la soldadura TIG, el equipo necesario para la soldadura MIG puede ser más complejo que el utilizado en algunos otros procesos de soldadura por arco.1 Además, el gas de protección inerte puede verse fácilmente afectado por corrientes de aire o viento, lo que limita su eficacia en aplicaciones al aire libre a menos que se tomen precauciones adecuadas para proteger la zona de soldadura.4 Finalmente, existe la posibilidad de perforación o quemado al soldar metales muy delgados si los parámetros de soldadura no se controlan con precisión.
Soldadura MAG (Metal Active Gas)
A. Proceso y Gases Activos:
La soldadura MAG, o soldadura con gas activo metálico, es un proceso GMAW que se distingue por el uso de un gas de protección activo.1 Los gases activos más comunes empleados en la soldadura MAG incluyen el dióxido de carbono (CO2) y mezclas de argón con CO2 o con oxígeno (O2).3 El CO2 es el gas activo más económico y proporciona una buena penetración del arco, especialmente en acero al carbono, aunque su uso puede generar una mayor cantidad de salpicaduras.3 Las mezclas de argón con CO2 ofrecen un equilibrio entre la penetración y la estabilidad del arco, siendo a menudo preferidas para la soldadura de aceros al carbono y de baja aleación.3 Las mezclas de argón con oxígeno se utilizan en la soldadura de acero inoxidable, con un contenido de oxígeno cuidadosamente controlado para mejorar las características del arco sin causar una oxidación excesiva.3 Es fundamental comprender que el gas activo reacciona con el baño de soldadura fundido, lo que influye en su metalurgia y en las propiedades finales de la soldadura.
B. Aplicaciones Comunes de la Soldadura MAG:
La soldadura MAG se utiliza principalmente para la soldadura de aceros al carbono y aceros de baja aleación.1 También se emplea en algunas aplicaciones de soldadura de acero inoxidable, utilizando mezclas de gases específicas.1 En cuanto a las aplicaciones industriales, la soldadura MAG es ampliamente utilizada en la industria automotriz para la fabricación de carrocerías y chasis.1 Es fundamental en la construcción de estructuras metálicas, como puentes y edificios.1 La industria naval también se beneficia de la soldadura MAG en la construcción y reparación de barcos.10 Asimismo, se aplica en la fabricación de maquinaria pesada y equipos industriales, en la fabricación de recipientes a presión y en la soldadura de tuberías.1 Finalmente, es un proceso común en trabajos de reparación y mantenimiento de estructuras de acero.
C. Ventajas de la Soldadura MAG:
La soldadura MAG ofrece varias ventajas notables. El costo de los gases activos, como el CO2 y las mezclas de argón con CO2, es generalmente menor que el de los gases inertes utilizados en la soldadura MIG.22 Proporciona una buena penetración del arco, lo que resulta especialmente beneficioso para soldar secciones de acero más gruesas.12 A menudo es más eficiente para la soldadura de materiales de mayor espesor en comparación con la soldadura MIG.12 La soldadura MAG se caracteriza por sus altas tasas de deposición, lo que permite realizar soldaduras más rápidas y aumentar la productividad.3 Es un proceso adecuado para aplicaciones de soldadura mecanizada y robotizada, lo que facilita su integración en líneas de producción automatizadas.1 Al igual que la soldadura MIG, se considera relativamente fácil de aprender y operar.
D. Desventajas de la Soldadura MAG:
A pesar de sus ventajas, la soldadura MAG también presenta algunas desventajas. Tiende a producir más salpicaduras en comparación con la soldadura MIG, lo que requiere un mayor esfuerzo en la limpieza posterior de la soldadura.1 En algunas aplicaciones, la calidad del acabado de la soldadura MAG puede no ser tan estéticamente agradable como la obtenida con la soldadura MIG.12 Existe un mayor riesgo de oxidación si el gas activo no se controla adecuadamente, especialmente en ciertas calidades de acero inoxidable.12 Además, el uso de ciertas mezclas de gases activos puede requerir un mayor nivel de habilidad por parte del soldador para lograr resultados óptimos.
Tabla 1: Comparación entre Soldadura MIG y MAG
Característica | Soldadura MIG (Gas Inerte Metálico) | Soldadura MAG (Gas Activo Metálico) |
---|---|---|
Gas de Protección | Inerte | Activo |
Gases Comunes | Argón (Ar), Helio (He) | CO₂, Ar+CO₂, Ar+O₂ |
Materiales Primarios Soldados | Metales no ferrosos (Al, Acero Inox) | Aceros al carbono y de baja aleación |
Calidad/Apariencia de la Soldadura | Limpia, a menudo mejor estética | Robusta, puede ser menos estética |
Nivel de Salpicaduras | Menor | Mayor |
Costo del Gas | Mayor | Menor |
Adecuación para Materiales Gruesos | Puede tener limitaciones | Generalmente mejor |
Facilidad de Aprendizaje | Generalmente fácil | Generalmente fácil |
Aplicaciones Comunes | Automoción (Al), Aeroespacial, Alimentaria | Construcción, Automoción (Acero), Naval |
VI. Similitudes Entre la Soldadura MIG y MAG
A pesar de sus diferencias fundamentales en el tipo de gas de protección, la soldadura MIG y MAG comparten varias similitudes importantes.7 Ambas son variaciones del proceso de soldadura por arco metálico con gas (GMAW).1 Ambos procesos utilizan un electrodo de hilo consumible que se alimenta de forma continua a través de una pistola de soldar.1 La necesidad de un gas de protección para salvaguardar el baño de soldadura de la atmósfera es común a ambos métodos.1 La configuración básica del equipo es similar, incluyendo una fuente de energía, un alimentador de hilo, una pistola de soldar y un cilindro de gas.3 Tanto la soldadura MIG como la MAG pueden realizarse en modos semiautomáticos o automáticos (robotizados), lo que las hace adecuadas para diferentes niveles de producción.1 Finalmente, ambos procesos ofrecen una alta productividad en comparación con otras técnicas de soldadura.
VII. Elección Entre Soldadura MIG y MAG
La selección entre la soldadura MIG y MAG depende de una serie de factores clave. En general, la soldadura MIG es preferible para la soldadura de metales no ferrosos como el aluminio, el acero inoxidable, el cobre, el magnesio y el titanio.3 Por otro lado, la soldadura MAG se utiliza principalmente para la soldadura de aceros al carbono y aceros de baja aleación.1 La calidad y el acabado deseados de la soldadura también influyen en la elección, ya que la soldadura MIG tiende a producir soldaduras más limpias y estéticamente agradables 1, mientras que la soldadura MAG puede generar soldaduras robustas pero con más salpicaduras.1 Los costos también son un factor importante, siendo la soldadura MAG generalmente más económica debido al menor costo de los gases activos 22, mientras que la soldadura MIG implica mayores costos operativos debido al precio de los gases inertes.22 El espesor del material a soldar también es relevante, ya que la soldadura MAG puede ser más eficiente para soldar secciones de acero más gruesas gracias a su mejor penetración 12, aunque la soldadura MIG se puede utilizar en una variedad de espesores.1 Finalmente, el entorno de soldadura debe considerarse, ya que el gas de protección utilizado en la soldadura MIG es más susceptible a las corrientes de aire.
Tabla 2: Gases de Protección para Soldadura MIG y MAG
Proceso de Soldadura | Tipo de Gas | Gases Comunes | Aplicaciones Típicas/Materiales |
---|---|---|---|
MIG | Inerte | Argón (Ar), Helio (He) | Aluminio, Acero Inoxidable, Cobre |
MAG | Activo | CO₂, Ar+CO₂, Ar+O₂ | Acero al Carbono, Acero de Baja Aleación |
VIII. Conclusión
En resumen, la diferencia fundamental entre la soldadura MIG y MAG reside en el tipo de gas de protección utilizado. La soldadura MIG emplea gases inertes, como el argón y el helio, que no reaccionan químicamente con el baño de soldadura, lo que la hace ideal para soldar metales no ferrosos y obtener soldaduras limpias y de alta calidad. Por otro lado, la soldadura MAG utiliza gases activos, como el dióxido de carbono y mezclas de argón con CO2 u oxígeno, que sí interactúan con el metal fundido, proporcionando una buena penetración y eficiencia en la soldadura de aceros al carbono y de baja aleación. Cada proceso presenta sus propias ventajas y desventajas en términos de costo, calidad del acabado, adecuación para diferentes materiales y espesores, y facilidad de uso. Por lo tanto, la elección óptima entre la soldadura MIG y MAG dependerá de los requerimientos específicos de la aplicación y las prioridades del proyecto.
Descargo de responsabilidad: Por favor, ten en cuenta que el contenido de esta entrada de blog ha sido generado con la ayuda de inteligencia artificial. Ni la empresa ni las marcas aquí presentadas asumen responsabilidad alguna por la exactitud, integridad o utilidad de la información proporcionada. Se recomienda a los lectores verificar la información de forma independiente antes de tomar cualquier decisión basada en este contenido.